Connected in the electrification age
The switch to electromobility is changing logistics chains worldwide. Swoboda, an automotive supplier based in Germany’s Allgäu region, sees this as an opportunity. To pursue it, DACHSER is helping the company reorganize its global supply chains.
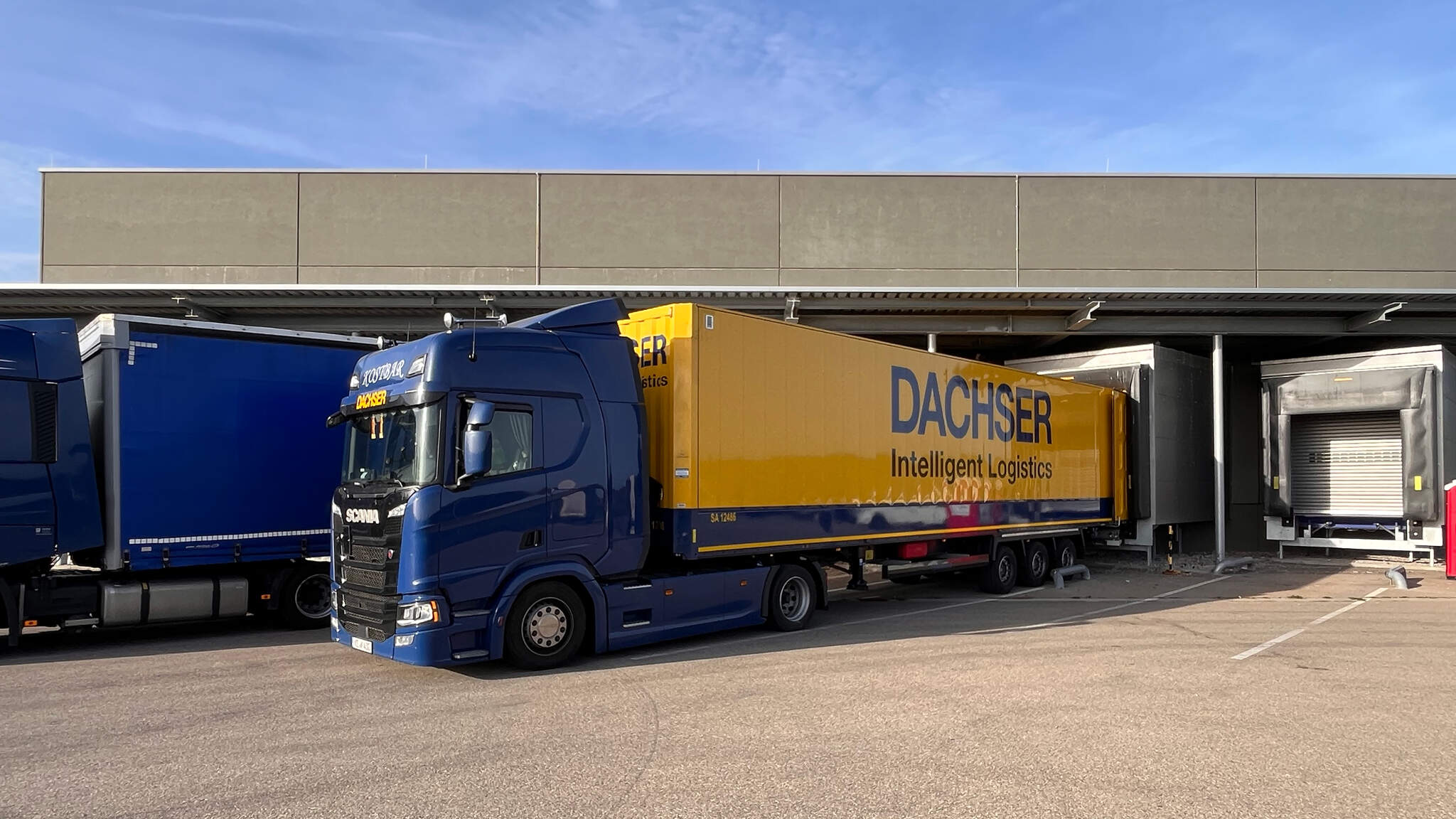
Momentum is building in the world of electromobility. According to Statista, annual revenue growth in the electric vehicle market is expected to reach around 10 percent by 2028. That same year, global sales are predicted to exceed 17 million units.
Even if some people would have liked the mobility transition to have covered more ground even faster, experts agree that the destination is clear. Megatrends such as electromobility, automated driving, connectivity, and new mobility concepts will further drive the transition from combustion engine to electric motor. This will bring about lasting change—not only for automotive manufacturers and suppliers, but also for logistics providers.
Among those who share this view is Dietmar Sirch, Head of Logistics Processes at Swoboda, an automotive supplier based in Wiggensbach near Kempten, Germany. “Now more than ever, logistics is expected to be flexible, stable, and fast,” he says.
Digitalization and transparency more important than ever
Like DACHSER, Swoboda is a family-owned company and global player with its roots in the Allgäu region. At twelve locations in six countries on three continents, some 4,000 employees develop and build sensors, ECUs, and powertrain components for the automotive industry.
Swoboda is active in market segments that are particularly well placed to benefit from this technological transformation. “We’ve had a hand in the transition to e-mobility for years now,” says Stefan Walgenbach, Head of Logistics at Swoboda’s Wiggensbach plant. The product portfolio and existing supply agreements with manufacturers are noticeably geared toward e‑mobility components. For many years now, Swoboda has been developing and manufacturing sensors and powertrain components for electric cars, e-bikes, cargo bikes, and e-scooters. Its goal is to make the technology safer, more convenient, and more energy efficient.
At its Wiggensbach plant alone, Swoboda manufactures around five million highly complex components and assemblies every month. These range from control instruments to large and heavy components. Every day, some one million components leave Swoboda’s plants worldwide. But the sheer quantity isn’t the only challenge facing a logistics provider.
"We need a partner that has a global presence and can seamlessly connect air & sea and road networks as well as optimize transports", says Dietmar Sirch, Head of Logistics Processes at Swoboda in Wiggensbach.
“The transformation is naturally compelling logistics companies to adapt even more,” Walgenbach says. He points out that the automotive sector has always been a decidedly dynamic market and it will continue to change to accommodate e-mobility. “Entirely new players are now entering the market, and they are positioned differently from the established manufacturers,” Walgenbach says. In the future, it will be necessary to supply parts and components to an even broader and more varied clientele.
Sirch believes that data exchange in particular will accelerate: “Our customers already expect to receive extensive information through digital channels (EDI) even before goods leave the plant, and as far as optimization goes, there’s no end in sight.” In addition, more and more customers will be requesting access to tracking for delivery vehicles. “They always want to know exactly where the truck is so they can plan production as precisely as possible,” Sirch says. All DACHSER swap bodies and trailers have been equipped with the necessary IoT devices for some time, which creates a high level of transparency in the supply chain.
And transparency, Walgenbach adds, is more important than ever. Last-minute changes to orders are happening with increasing frequency. Production suppliers are still feeling the effects of recent disruptions to supply chains and bottlenecks for electronic components such as semiconductors from the Far East. Manufacturing requirements can change incredibly quickly. “Order volumes and delivery deadlines for some customers can change overnight—10 pallets suddenly become 50,” Sirch says. Swoboda has to be ready to respond, and so does DACHSER. “It’s a major challenge for the supply chain as well as our own inventory optimization,” Walgenbach says. As Swoboda promises its customers security of supply, the company must have a reliable logistics provider that is equal to the task.

DACHSER as a global logistics partner
DACHSER’s suitability for fulfilling these exacting requirements is demonstrated by the two companies’ longstanding collaboration, which began back in 2005. “Keeping goods flowing efficiently along the supply chain calls for seamless collaboration between logistics providers and automotive customers. It’s about more than simply moving products. It’s really about creating trust and achieving success on the path of mobility,” says Christian Fackler, Sales Manager at DACHSER’s Allgäu logistics center. Swoboda first commissioned DACHSER to handle just transport and freight forwarding, but the logistics company is now providing an extensive range of services including warehousing and customs clearance. What’s more, DACHSER has expanded the “Interlocking” of European Logistics and Air & Sea Logistics to create a reliable basis for imports and exports to and from Swoboda plants in China and Mexico. “There are also more projects in the pipeline for route optimization, needs-based provision of intermediate products for manufacturing, and the digitalization of shared processes,” Fackler says.
All this is made possible thanks to the continuous optimization of supply chains that has taken place over the course of the collaboration. In 2016, for example, Swoboda’s logistics team noticed that stamped strips from the plant in the Czech Republic were being transported to Pforzheim near the Franco-German border for further processing. They were then taken back to the Czech Republic, where they were stored until needed at the Wiggensbach plant in Allgäu. All this made for a protracted and costly procedure. Deliveries to the Allgäu plant now fall within the DACHSER network. “In addition to increasing our flexibility, the short distances really benefit the environment,” Walgenbach says. Today, DACHSER already handles over 80 percent of Swoboda’s European transports.
To prepare for future changes, Swoboda wants DACHSER’s help to systematically further optimize its supply chains. “One day we’ll be operating with entirely different volumes and pickup frequency,” Sirch says. Moreover, it will be even more important to reduce CO2 emissions from transports. This is the rationale behind making more groupage shipments. “We’ll establish synergies across plants, for instance to optimize the flow of materials from the Schorndorf and Fürth locations in southern Germany to our locations in the Czech Republic and Romania,” Sirch says. But he’s also aware that reducing environmental impact while also offering special rush deliveries constitutes a major challenge, one that calls for seamless interaction between the systems used by Swoboda and its logistics provider.
This will be the basis upon which Swoboda and DACHSER will set about reorganizing the automotive supplier’s global logistics chains. Up to now, each plant has followed its own concept for warehousing and inventory scheduling. However, since semiconductor manufacturers in Asia plan their production activities well in advance, contractors are sometimes unable to change their orders up to six months prior to delivery—a time period referred to as a “frozen zone.” But as some of Swoboda’s customers change their production planning at short notice, the company requires logistics solutions that can accommodate this reality. These include ways of quickly and cost-effectively transporting electronic components from suppliers in Asia and overseas in order to shorten delivery times. “We’re looking to consolidate our sources of electronic components in Malaysia, Indonesia, Japan, and China,” Sirch says. What Swoboda is planning is a streamlined global network of warehouses that will supply both the company’s own production activities and its customers. “That means we need a partner that has a global presence and can seamlessly connect air & sea and road networks as well as optimize transports. DACHSER’s going to have plenty to do,” Sirch says with a wink, quickly adding: “After all, quality and delivery reliability are what we value most.”
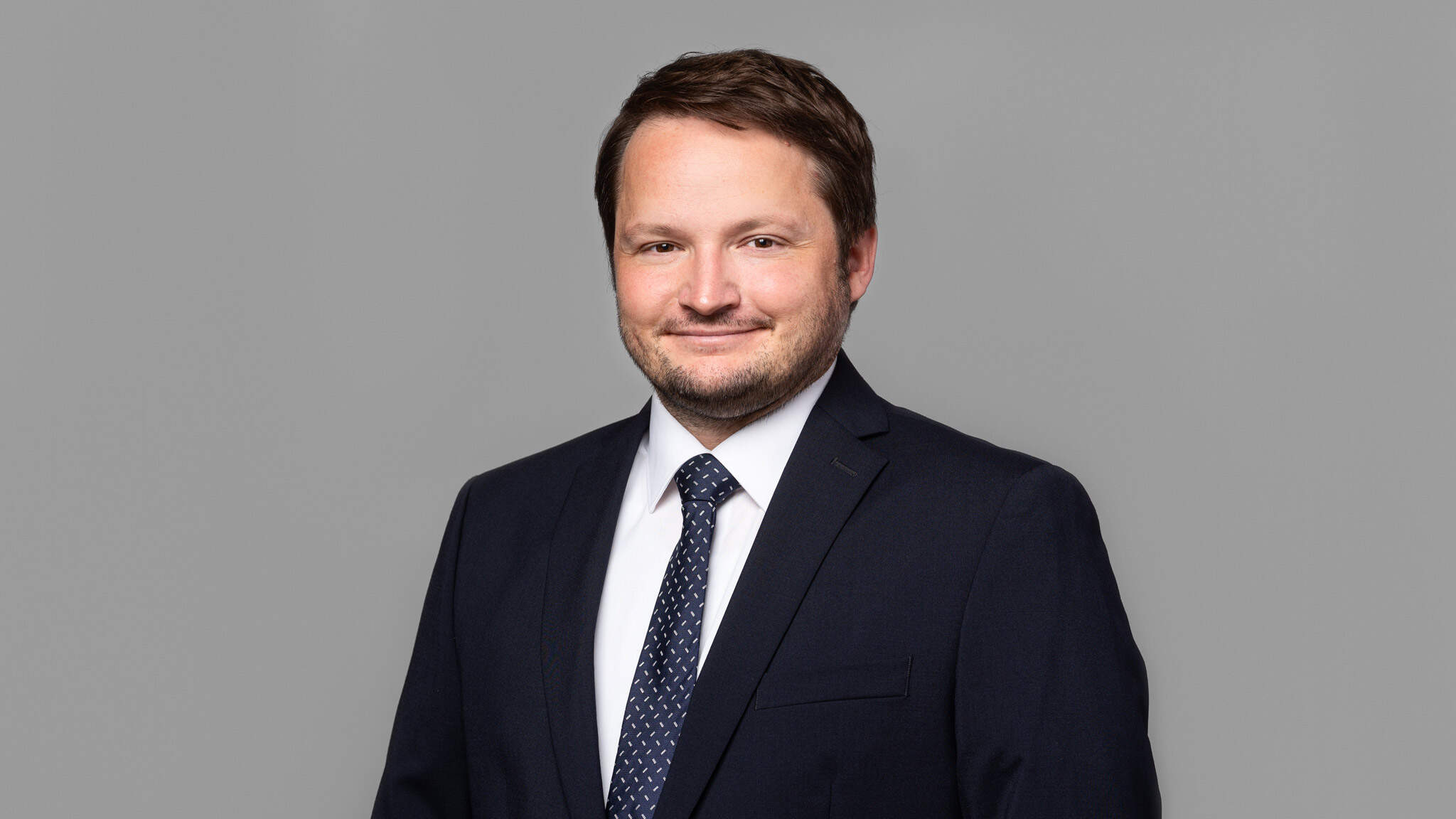