Elephantine strength in the warehouse
Despite progress in automation, many jobs still have to be done manually—especially in warehouses. Unloading or repacking goods by hand is a regular occurrence. DACHSER is now harnessing innovative technology to safeguard the health of its employees.
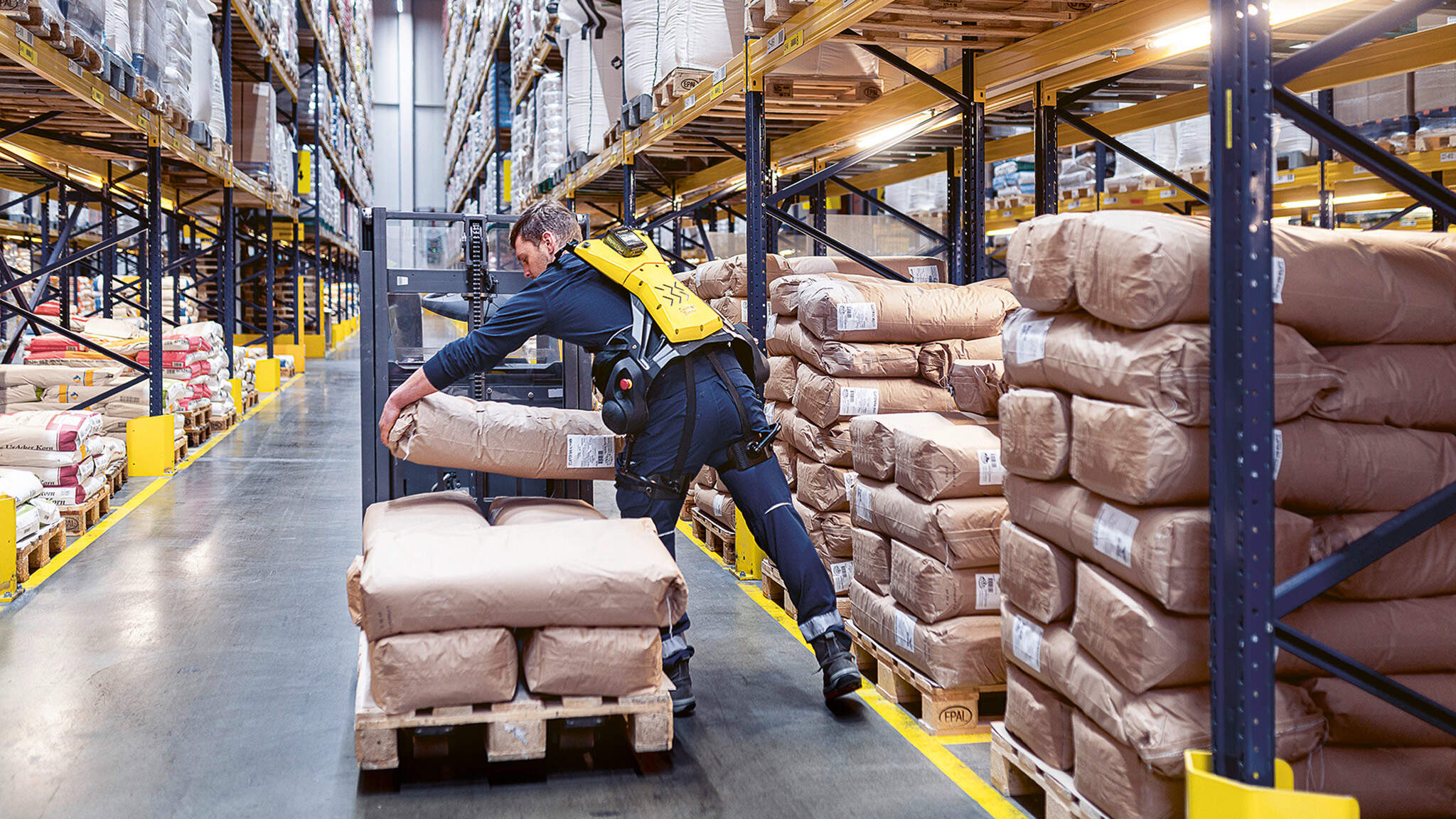
Attached to the mighty carbon frame resting on Patric Dandl’s hips is a small display. He taps it a couple of times: “It seems that today, I’ve already repacked two elephants,” says the 31-year-old Deputy Shift Leader, who works at DACHSER’s warehouse in Langenau near Ulm in southern Germany. On peak days, he can lug around up to 8,000 kilograms in a single shift.
Dandl is in fact not a zookeeper, moving massive pachyderms around their enclosures. Instead, he works in a warehouse, where he moves heavy loads with the help of a new kind of exoskeleton. On any given day, employees picking sacks of goods in the food warehouse will together move up to 60 metric tons from one pallet to another—not exactly easy on the back. After a while, these 25-kilogram sacks of baking ingredients and mixes start to add up.
“My colleagues who do the lifting don’t have a problem with that,” says Michael Trunk, Contract Logistics Manager Food Logistics at DACHSER’s Ulm logistics center, quickly adding: “At least, not the younger ones.” But physical complaints can multiply with age. To provide some relief, for a long time DACHSER has been investigating how it can support its employees who perform the manual—and often physically demanding—warehouse tasks that are still essential.
This relief comes from state-of-the-art robot technology familiar from science fiction, but used mainly in the healthcare sector. Such external support constructions have been popular in that area for quite some time. They help nursing staff lift and move patients, for example, and support surgeons who have to stand for hours on end in the operating room. In the future, they will also help people suffering from physical impairments or muscle weakness to regain their mobility. And now, they are also being used more and more in industry.
Wearable robots
Following successful tests, DACHSER is now using active, AI-supported exoskeletons at certain locations, including the Langenau branch. These wearable robots made by Augsburg-based robotics company German Bionic are donned like a backpack and held in place by straps at the chest and thighs.
Back in 2019, DACHSER launched its first pilot projects involving exoskeletons made by other manufacturers. Equipped with mechanical suspension systems, these passive devices simply transfer the forces at play. By way of contrast, the Cray X active exoskeletons currently in use feature battery-powered motors that help the wearer lift and carry heavy objects.
“Exoskeletons help prevent both unhealthy strain and workplace accidents. That’s sustainability.”
These wearable robots don’t exactly turn DACHSER employees into superheroes who can then effortlessly lift any object no matter how heavy. Dandl even sounds like a robot when he moves, but that’s due to the mini-motors that emit that characteristic soft hum as he moves along the warehouse’s high-bay racks. Instead, the technology reinforces the movements Dandl makes. If he bends over to pick up a sack from a pallet, the exoskeleton ensures that he doesn’t bend his back too much. The device then registers when he begins to straighten up and helps him do so.
Wearers can decide for themselves how much ergonomic support the exoskeleton should provide. “Set to 100 percent, the device will pull me fully upright as soon as it notices that I want to straighten up,” Dandl says. But he thinks that’s going too far. Even though the exoskeleton provides support, Dandl feels like he’s controlling it and not the other way around. Wearing the device doesn’t mean the operator’s muscles no longer have anything to do. But it does make lifting a 30-kilogram object as easy as lifting a 5-kilogram one, which relieves the burden on spinal discs, the shoulders, and the back muscles. Less pressure on the discs translates into fewer injuries.
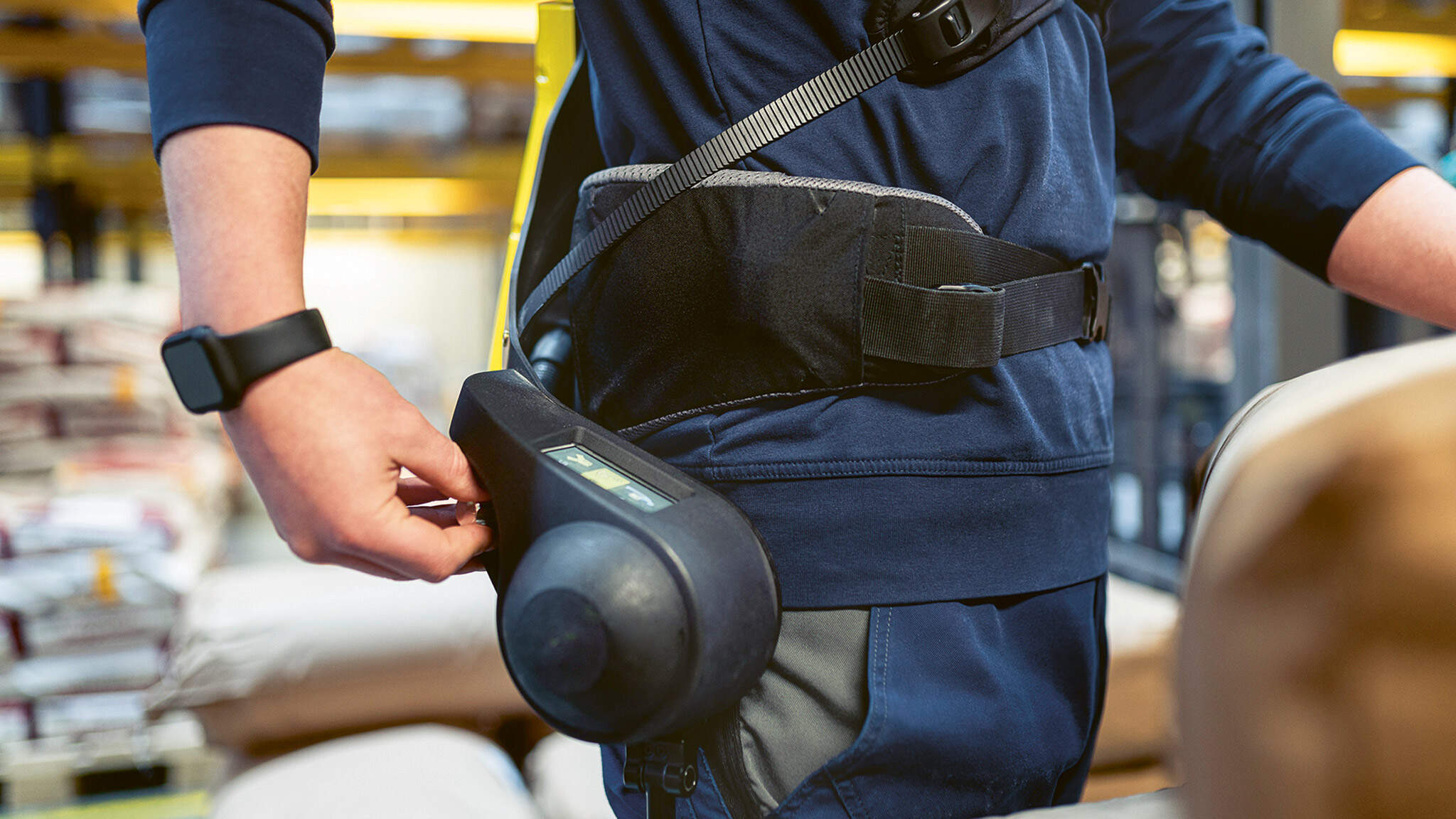
A cool technology experience
For Michael Trunk, preventing injuries is a major concern. Since it’s becoming harder and harder to interest young people in a warehouse position, the workforce is getting older. “DACHSER is using this technology because we want to keep people from overdoing it and prevent workplace accidents. Wearing an exoskeleton means employees are less likely to adopt a potentially harmful posture when lifting heavy objects,” he says. What’s more, the device has a certain coolness factor. “It’s a great way of engaging with young people at career and apprenticeship fairs, and shows them that working in a warehouse also means getting to try out the latest technology,” he adds. Exoskeletons automatically make the work much more interesting.
Dandl confirms the practical benefits: “Exoskeletons don’t necessarily mean working faster,” he says, “but they do provide a level of relief that you really notice by the end of the day.” Matthias Nitz, Deputy Warehouse Manager in Langenau, notices that such experiences are increasing acceptance of the exoskeleton. For his part, Dandl had no trouble getting on board with the new technology. “You get used to wearing an exoskeleton really quickly,” he says. The device’s tight-fitting backpack means he has to change his sweaty T-shirt a little more often, but he thinks that’s a small price to pay. What doesn’t have to be changed out during a shift is the device’s small battery pack.
Dandl notes one drawback: “The device makes you bulkier. In the beginning, you tend to bump into things more often.” Working with the exoskeleton does take some getting used to. To prepare warehouse employees for working with the exoskeleton for several hours at a time, they are currently receiving in-depth training to acclimate them to this motorized support. Representatives from German Bionic are also frequent visitors to the warehouse, providing practical tips and gathering data for further development.
DACHSER’s Langenau branch is currently using two exoskeletons in its warehouse for picking and repacking pallets. Trunk says that there are also plans to use these devices when unloading containers. Each device is used by multiple employees; each person can store and retrieve their individual settings by entering their PIN. At the end of each shift, the operators can see how many kilograms more they would have carried. “It’s usually quite a few elephants,” Dandl jokes.
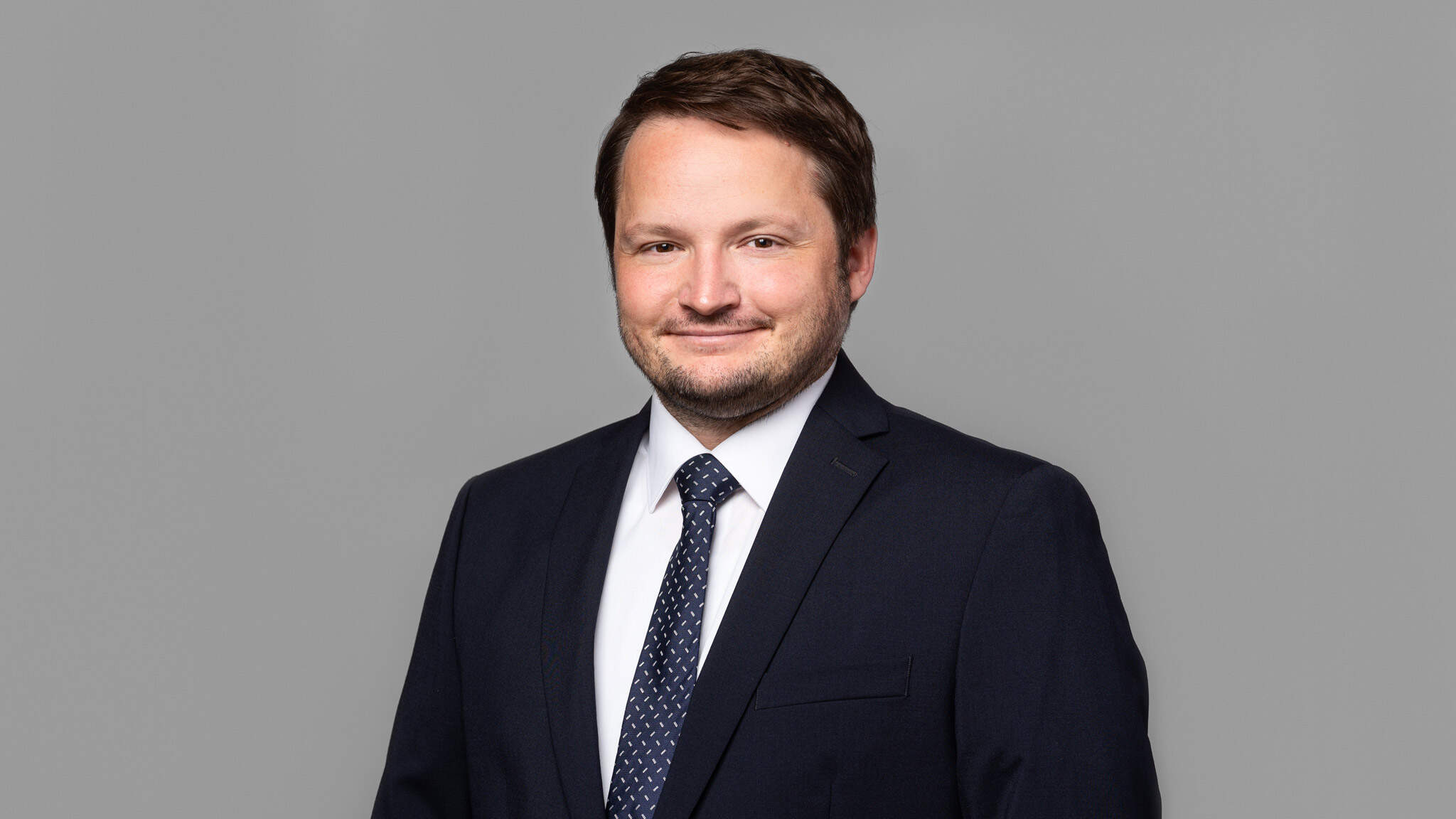