Going round in circles
It’s the quiet, retiring type that quite literally sinks into the floor. Definitely not out of embarrassment, though, because the underfloor conveyor system, or UFCS for short, is one of the most valuable and productive tools for dealing with high transport volumes. That is why at DACHSER, too, it doggedly keeps on turning round after round, as an effective additional tool to supplement forklifts or stackers.
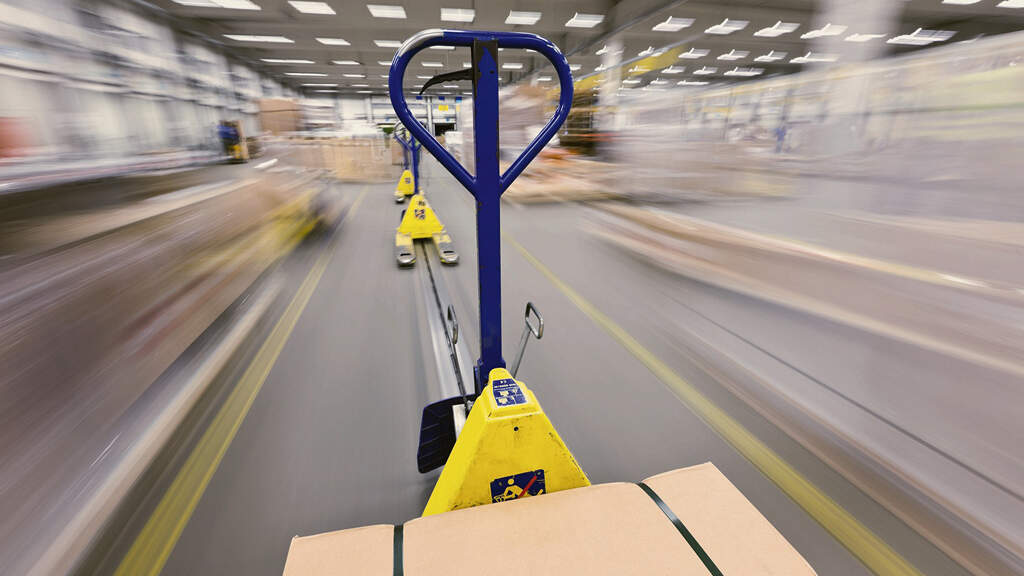
The UFCS is a chain which runs on a fixed track embedded in the hall floor. The advantage of this is the constantly high distribution rate. It reduces the distances for staff and lowers noise levels in the hall. Its set route does not necessarily mean less flexibility and possibilities for variation though.
“DACHSER has deliberately and systematically opted for the circular shape in order to establish standardized organization. This allows us to transport the goods on an outer track after unloading,” explains Thomas Schmalz, Head of Production Management at DACHSER: “The large radius increases the chain capacity. Add to this the very efficient use of space for goods handling, individually adjustable entry and exit points for the goods and not least low investment, maintenance and servicing costs to the list of benefits provided by the circular shape.” In each individual case checks are run to determine whether using an underfloor conveyer chain at a particular DACHSER branch makes economic sense. This entails a detailed process cost calculation, which even includes real data from the Transport Management System Domino. “We can compare the costs for conventional production and production with UFCS for each hour of work and make a decision on this basis”, explains Schmalz.
From Stockholm to Barcelona – and back
26 chains are currently in active operation at the DACHSER Business Line European Logistics; the pilot system of the type used until today went into operation at the Allgäu, Memmingen Logistics Center in 1993. This kind of technology, however, has had a long-standing tradition within DACHSER. The company inaugurated its first underfloor conveyor system as early as 50 years ago in the German branch at Wangen, Allgäu. Being an ultra-modern facility at that time, the branch was additionally equipped with data processing (Hollerith machines by IBM) and radio communication to the distribution vehicles.
In general, the larger the hall, the longer the chain. The longest at 470 meters is currently in place at the Ostwestfalen-Lippe Logistics Center in Bad Salzuflen. In total DACHSER boasts 10,000 meters of chain, which is the equivalent of the take-up capacity of around 2,350 hand pallet trucks.
On the chain, a hand pallet truck does around 5,500 kilometers a year—that’s as far as going by truck from Stockholm to Barcelona and back once
“On the chain, a hand pallet truck does around 5,500 kilometers a year—that’s as far as going by truck from Stockholm to Barcelona and back once,” says André Bilz, Team Leader Fleet Management Terminal Equipment at DACHSER. This places high demands on components such as the hydraulics, tow hooks, or wheel axes or bearings. “We carried out projects and test series on this with the individual manufacturers to set the quality standards required for DACHSER,” Bilz states.
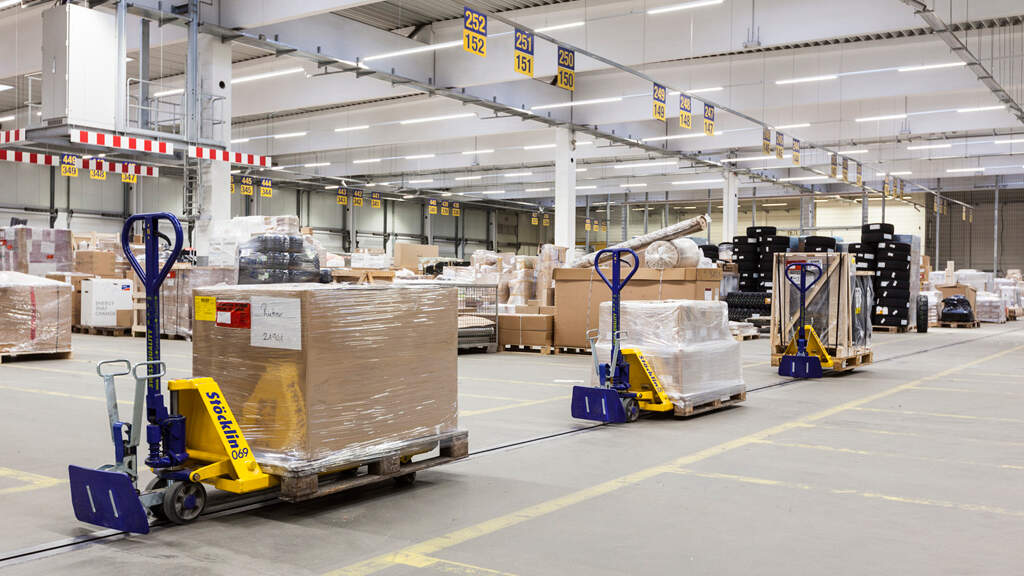
Five rotations per hour
The chain’s speed can be regulated in certain areas; at DACHSER it is usually set at 28 meters per minute. This means, for example, that the system in Bad Salzuflen manages a whole five rotations per hour. But completing a rotation is not the aim of the chain. “We wouldn’t be DACHSER if there wasn’t a whole lot of ‘Intelligent Logistics’ behind this,” Thomas Schmalz grins. There’s the bay management for example: each incoming loading list, on the basis of the shipment it contains, is used to calculate the distance of the—pre-defined—unloading bay to the respective storage bay and the total distance in meters per bay. What is more, an intelligent arrangement of the feed-in points increases the capacity performance of the UFCS by 60 per cent.
This enables the travelling time of the goods in the chain to be minimized even before the pallets arrive in the hall. So the goods don’t usually get to enjoy the feeling of going full circle. And that’s how it should be, too, because the shorter time spent on the chain by a shipment unit lowers the risk of damage considerably. This doesn’t just save time and increase flexibility, it is also fine-tuned to the daily volume in each case. “The pallets moving along the chain will be part and parcel of day-to-day life at DACHSER for a long time to come”, Thomas Schmalz is sure.
The savings made in equipment costs contribute to this as well of course. These are thanks to the smaller fleet of industrial trucks required, the longer intervals between maintenance and servicing and less wear and tear you get with the underfloor conveyor system. This means that the lifespan of one of these “continuous conveyors” is two to three times longer than lift trucks.