Heavyweights on tour
Shipping 138 metric tons from Brazil to Mexico—DACHSER Air & Sea Logistics organized the transport of an oversized machine for automotive manufacturing. After dismantling the machine into 14 parts, the largest piece alone—a compressor—weighed 125 metric tons. The journey was first made by heavy-lift cargo transport through the Brazilian state of São Paulo, then by container ship to Mexico, where another truck took over again for the last leg to the production plant in central Mexico.
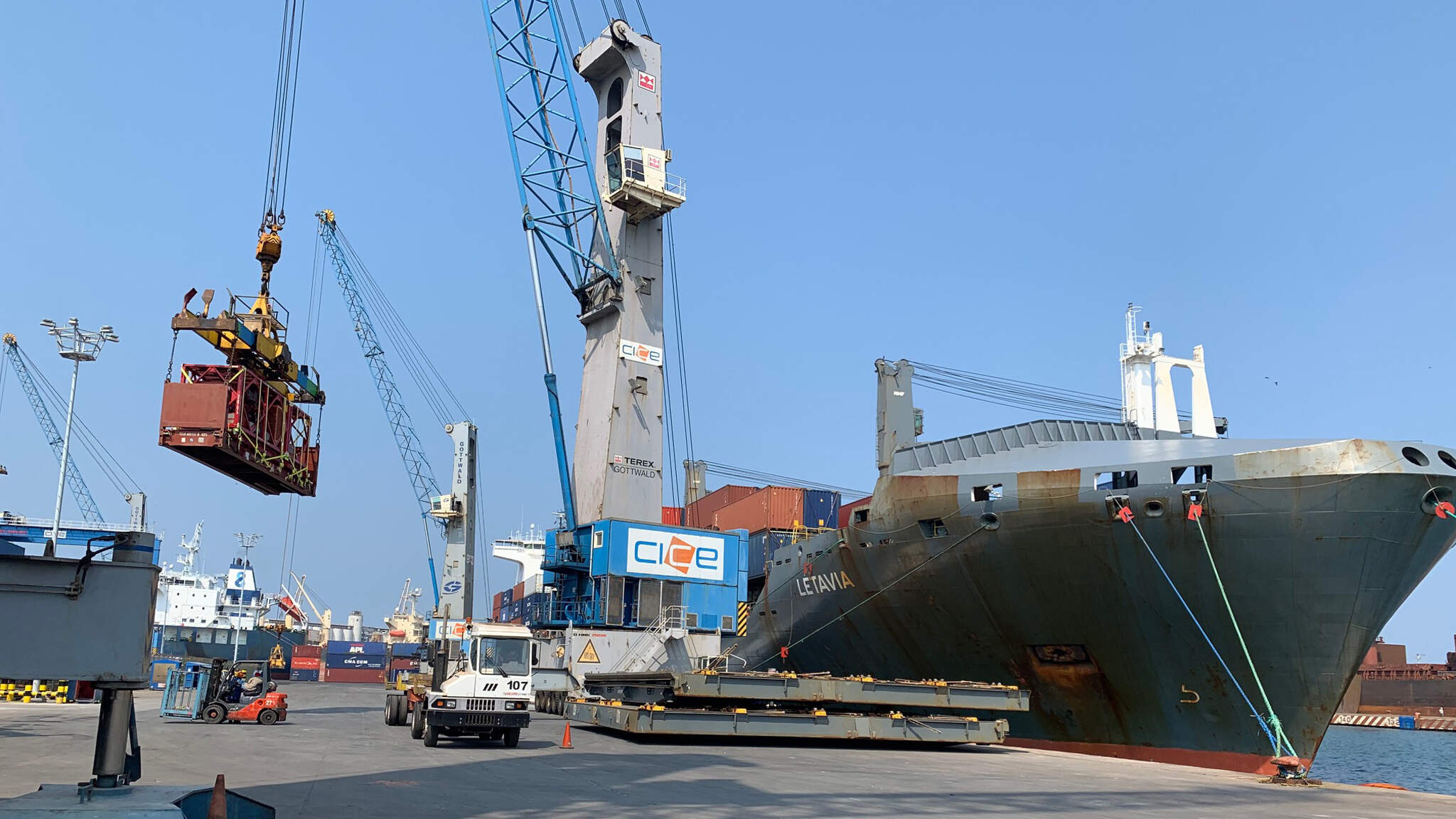
At the end of April, DACHSER shipped a total of 138 metric tons of oversized automotive manufacturing machinery and components from Jundiaí in Brazil to Silao in Mexico. This project required the experts at DACHSER Brazil, DACHSER Mexico, and DACHSER USA to draw on their entire logistics know-how. “We regularly support our customers with their complex logistics challenges,” says Guido Gries, Managing Director DACHSER Americas. “Complex heavy-lift projects always pose special challenges. In addition to expertise, what they really call for is innovative thinking.” For the customer, DACHSER’s experience in project shipments and its strong network within Latin America were decisive factors in choosing the company as its logistics partner.
First leg: through Brazil on a platform trailer
From the outset, this transport project posed a great challenge: the machine was still in use and was located in a pit about 5.5 meters deep. DACHSER commissioned one of its local partners, a hoisting equipment specialist, to lift the components out of the pit. Next, the machine components had to be disassembled into 14 parts of different sizes. Speed was also important, as the time at which the machines left the factory in Brazil naturally affected the time at which the delivery arrived in Mexico.
The journey continued on a multi-axle platform trailer on previously approved routes to the port of Santos. Due to COVID-19 restrictions, there was no police escort, and the cargo was permitted to travel through partly mountainous terrain only between the hours of 11 p.m. and 6 a.m. In total, it took seven days for the heavy-lift cargo to travel the almost 160 kilometers from Jundiaí to the port of Santos.
“When planning a project transport of this size, you have to take many factors into account. But we knew from the very beginning that the decisive element was going to be communication,” says João Caldana, Managing Director DACHSER Brazil.
“The project called for the services of many different parties: from the bodies issuing the authorizations, through brokers and local authorities, to the shipping company and our road transport partners—so to ensure smooth implementation, it’s crucial to keep everyone up to speed and fully involved.”
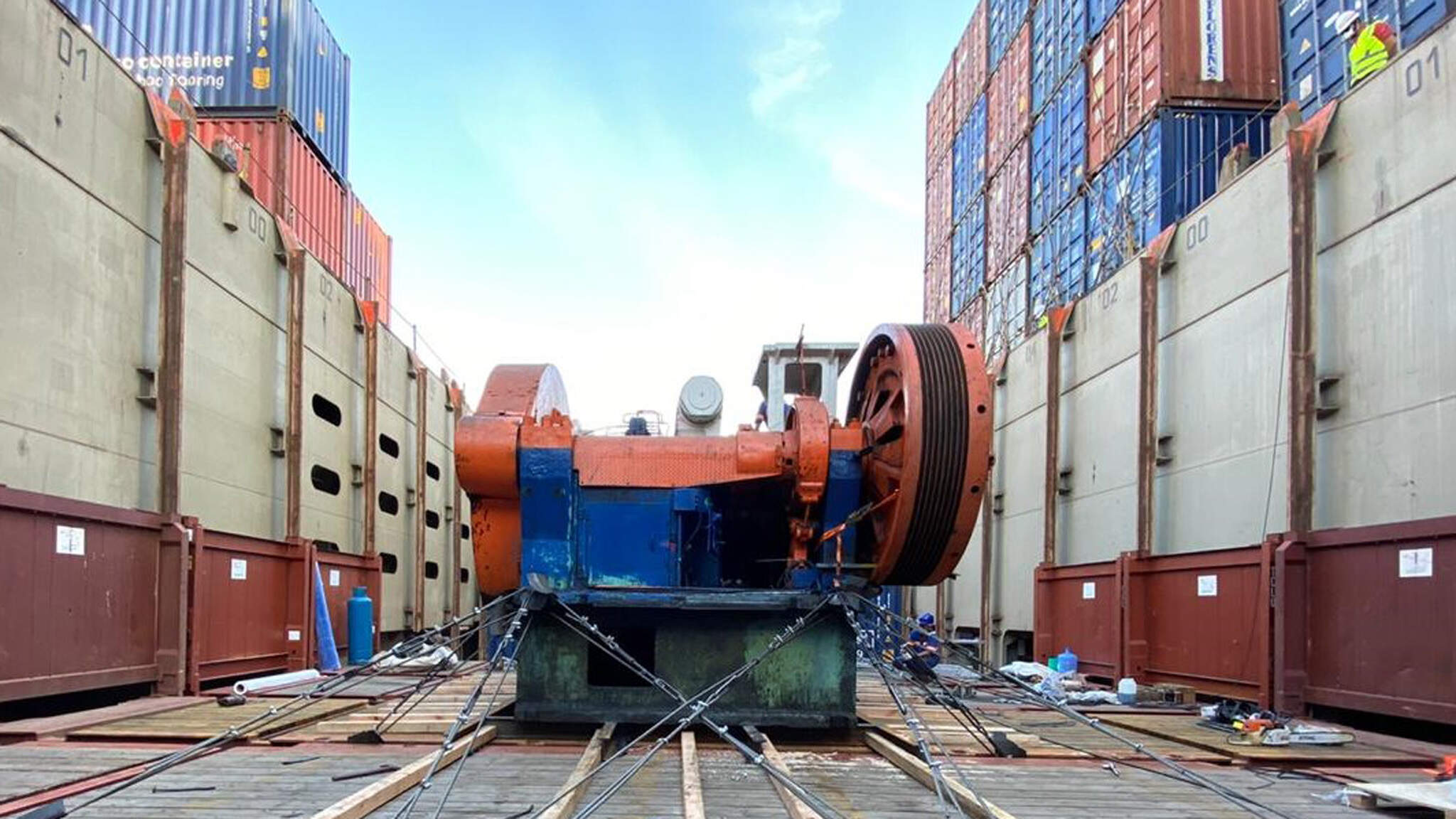
By container ship to Mexico
When it came to arranging onward transport by ship, the choice was between ro-ro services or break-bulk services. After a thorough analysis of the costs, transit time, and, above all, safety of transporting the cargo, DACHSER decided on a bulk break solution break-bulk solution. This offers the sender flexibility in loading and off-loading as well as in storage and unloading, while ensuring efficiency in meeting costs and delivery deadlines.
In cooperation with the CMA-CGM shipping company, the DACHSER Brazil team identified the type of ship required to transport and store the bulky equipment. They opted for a container ship as the fastest and most efficient option. The cargo was stored in the belly of the ship on flat rack containers and a specially constructed platform.
In the port of Santos, another challenge awaited: in order to avoid potential collisions with the terminal’s gantry cranes while loading the heavy cargo, the DACHSER team arranged for a floating crane, which enabled the crew to load on the opposite side of the ship, thus bypassing the gantry cranes. This required good weather conditions to ensure precise weight distribution throughout the lifting process.
Effects of Covid-19 felt here, too
After 30 days at sea, the cargo arrived in the Atlantic port of Veracruz in Mexico on May 3. It was the end of a Mexican holiday weekend, but the DACHSER Mexico team’s well-coordinated plans ensured that the holiday didn’t slow down onward transport. The cargo was transferred directly from the ship to a modular truck that was waiting next to the ship for the oversized cargo. Customs clearance was then carried out the following day.
Similar to the first leg of the journey in Brazil, the cargo was transported by road from the port to the production plant with additional precautions in place due to the coronavirus pandemic. While the pre-authorized routes on the country roads were approved for this oversized cargo, the schedule had to contend with temporary road closures, predetermined time slots, and a lack of local police escorts. The 700-kilometer journey from the port of Veracruz to the customer’s plant in Silao in central Mexico then took three more days. Once the heavy-lift cargo had reached its destination, three cranes finally unloaded it from the truck.
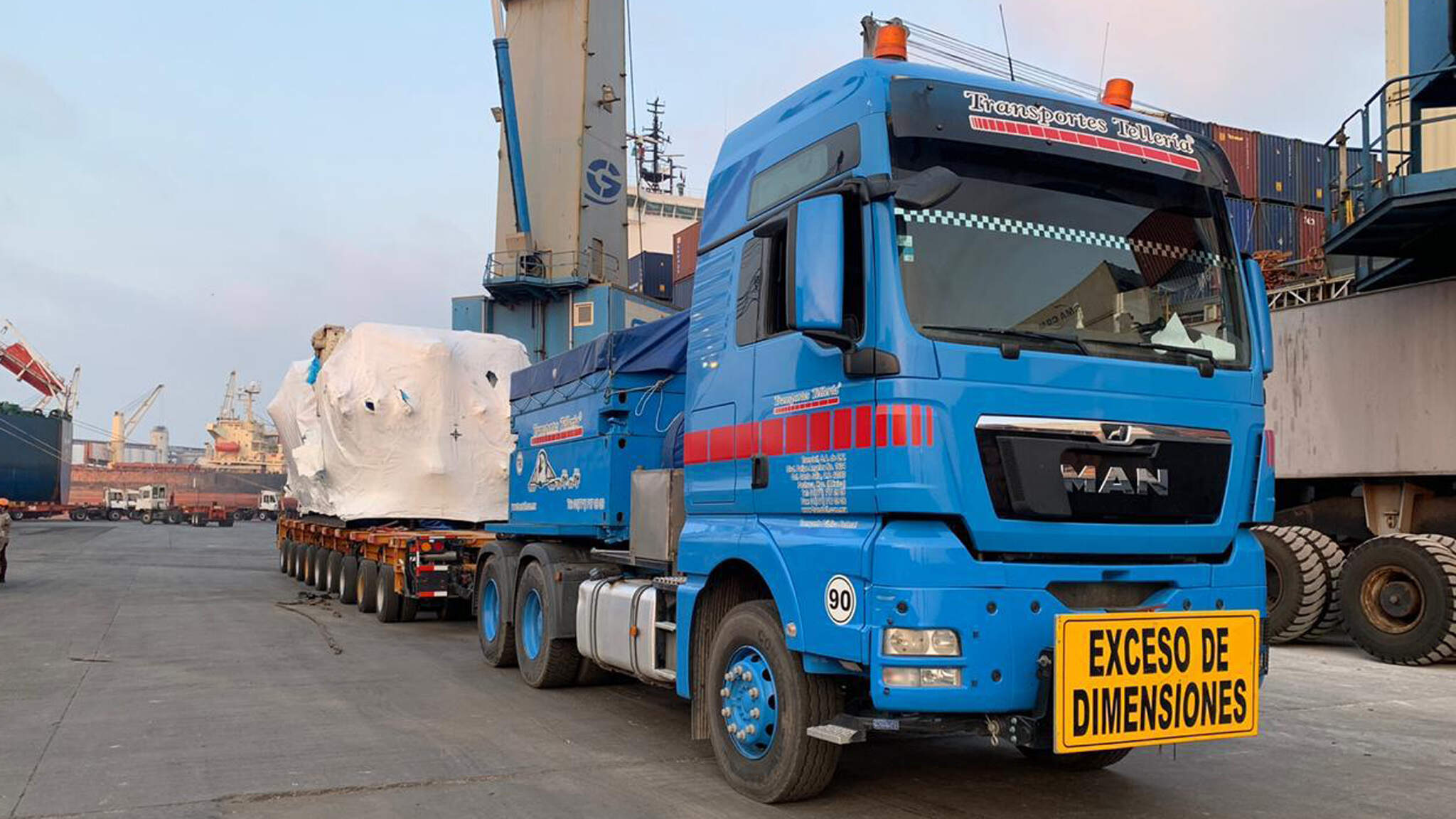
Working together to achieve the seemingly unattainable
“To successfully implement a project of this magnitude is a major achievement—especially in the middle of a global pandemic,” says Edgardo Hamon, Managing Director DACHSER Mexico. “It shows how well the various country organizations within the DACHSER family work together to achieve the seemingly unattainable.”