Logistics out of the printer
3D printing is no longer sci-fi: metal parts for aircraft, for example, are already now no longer being welded together out of individual components – the entire subassemblies are already being printed out. Mass production appears to be just a matter of time. This is opening up a new world of business for certain branches of industry – but does this go for logistics as well?
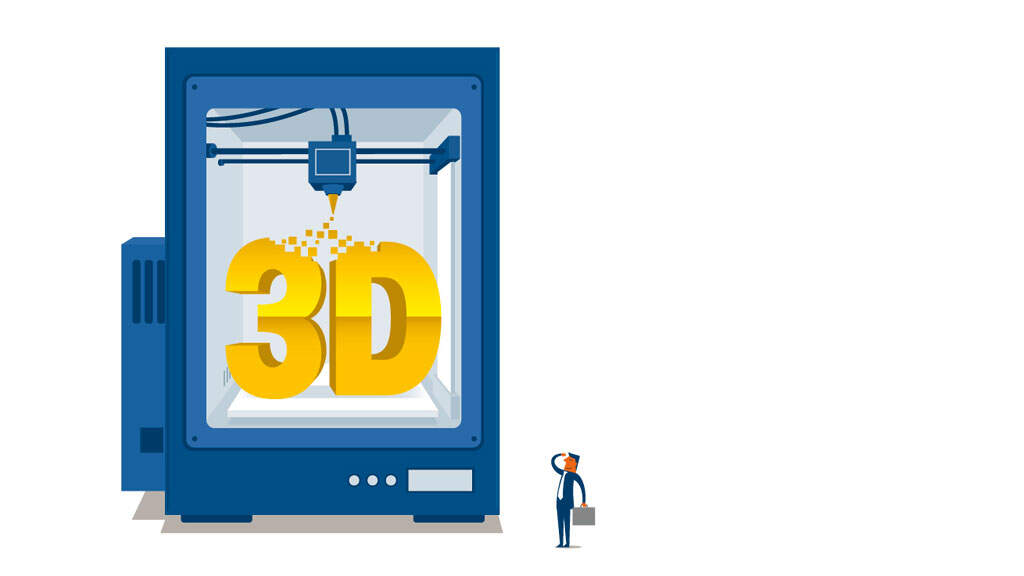
Smart networking of production units via the Internet – in short Industrie 4.0 – is the talk of the town at present. The digitization of their production is revealing untold opportunities for manufacturing. Potential that the logistics sector is already harnessing now: networking physical objects with digital supporting information in order to create transparency and optimize business processes. This pioneering role is being driven – as mundane as it sounds – by day-to-day business: a logistics service provider has to know at all times where the goods of its customers happen to be. Its playing field is at the same time the whole world. “Given this, the development of cyber-physical systems is pure and simple a must. Logistics service providers like DACHSER that have invested in their IT are therefore well prepared for the digitization strategies of industry,” is how Andreas Froschmayer, Corporate Director Corporate Development, Strategy & PR, sums it up.
Whatever you can weld, you can print
In the context of digitization, 3D printing also warrants attention as one of the most intensely discussed topics in the logistics branch at present. 3D printing is in principle a welding and smelting process. The raw material, metal, is welded layer by layer in powder form with a laser or electron beam. The term for this frequently used—additive layer manufacturing—is derived from the layer model. For business enterprises in the manufacturing sector, 3D printing means a veritable quantum leap: sub-components can be produced in one piece, eliminating individual parts, entire production steps and thus tool costs in one fell swoop. This also has repercussions for logistics in the form of less complex supply chains.
For business enterprises in the manufacturing sector, 3D printing means a veritable quantum leap: sub-components can be produced in one piece, eliminating individual parts, entire production steps and thus tool costs in one fell swoop
The global market for 3D printing is skyrocketing with growth rates of around 30 percent per year. Branch experts estimate that between two and five percent of transports along the Asia-Europe trade route will be lost by 2020. Transport volumes for finished products and sub-components may also decline. But what at first glance sounds like a doomsday prophesy for the logistics branch holds out enormous potential—if logistics service providers are successful in latching onto industry’s value-creation chain in an intelligent manner. The first business models to this end are currently under development. These range from the transport of metal in powder form all the way to parallel strategies for 3D printing and traditional spare parts logistics, as this technology would only appear to make sense for around 20 percent of manufacturing—at present.
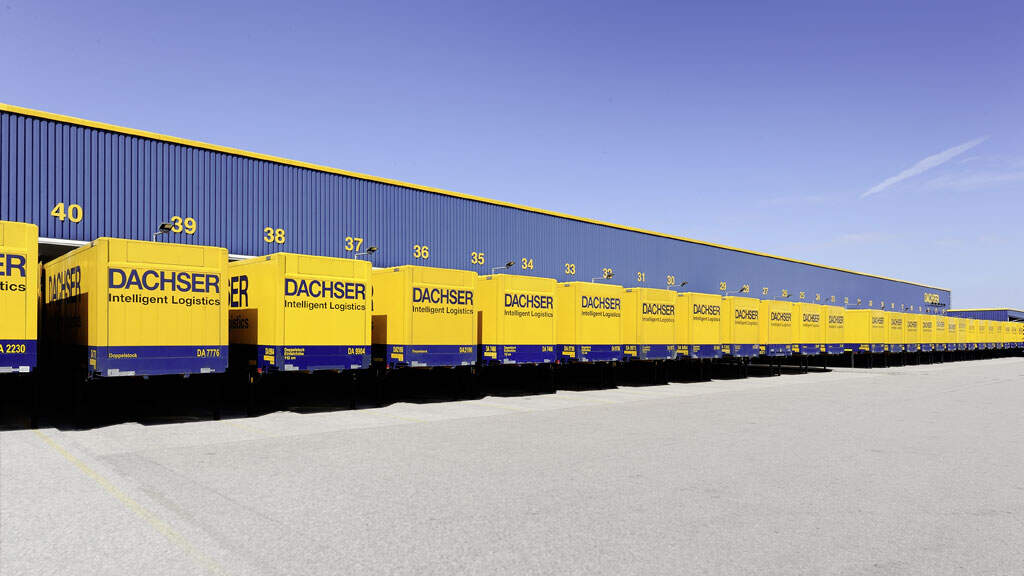
Expanding the range of logistical services in the network
3D printing also offers DACHSER the possibility to expand its range of logistical services over the next few years while opening up new business opportunities. Possible business models are being researched at present within the framework of company-wide innovation management. “By the same token, it is not beacon projects that stand at the forefront, how-ever, but rather value-generating use in the DACHSER network,” explains Dr. Andreas Froschmayer.
3D printing technology is still far from being perfected. Too many issues remain unresolved, ranging from the price development for laser and electron ray printers all the way to disposal of printing material. In addition, there are some very critical aspects such as property rights, product liability, quality control and certifications. “There is thus still a lot of homework to do,” according to Andreas Froschmayer. “Above all, there are still too few viable business models revolving around 3D printing. This is where industry is called upon to take the initiative.”