Programming the future
In this increasingly complex world, providing the chemical industry with first-class groupage logistics means continuously enhancing the services on offer. AI applications play a major role in this perpetual and lasting transformation. Michael Kriegel, Department Head DACHSER Chem Logistics, explains AI’s potential for logistics and how is it helping DACHSER to overcome current challenges.
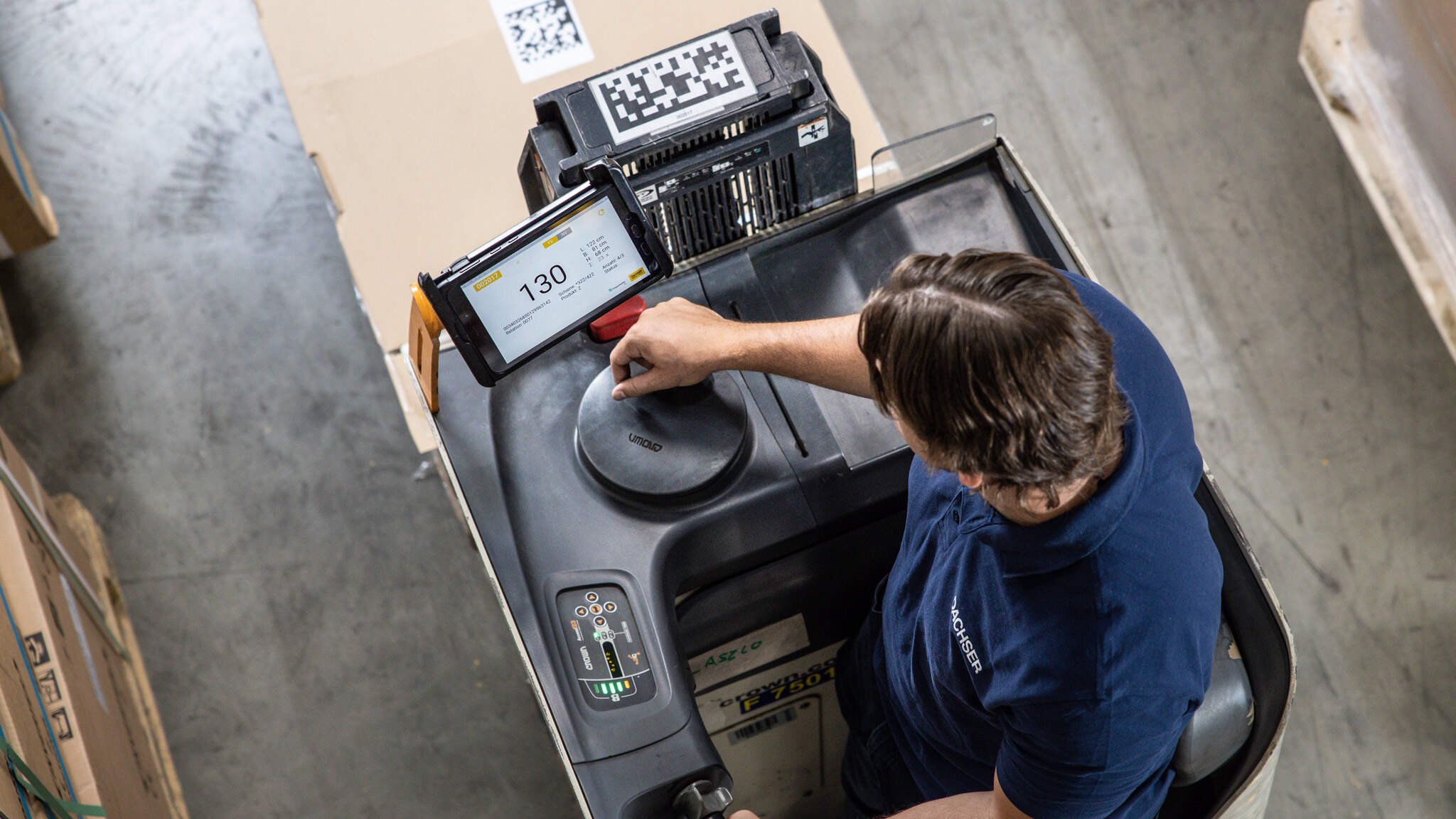
DACHSER made digitalization a priority early on, and by introducing the SSCC barcode and highly integrated core systems, the company helped shape the digital course logistics has taken. Today, the top items on DACHSER’s digitalization agenda are machine learning and artificial intelligence (AI).
The logistics industry now urgently needs digital transformation to ensure quality and to tackle challenges such as the shortage of drivers and other skilled workers. Moreover, the industry is being called upon to further pick up the pace when it comes to adopting new technologies and to incorporate societal megatrends such as digitalization, urbanization, e-mobility, and connectivity—which are changing the way we live—into its development activities. This calls for a strategic mindset and a firm grip on the controls, because it all comes down to actively shaping the future by anticipating what will be required. At DACHSER, we’re exploring three key use cases for AI applications that will also benefit our customers in the chemical industry: groupage handling itself, planning processes, and reducing emissions.
The digital transformation of groupage logistics
Groupage logistics is a fundamental factor in the competitiveness of industrial economies and thus also of the chemical industry. Here, too, the volumes of goods loaded onto pallets and into big bags are decreasing, meaning it makes sense to share cargo space with other consignors. This is the only way to deliver goods quickly and cost-effectively while keeping CO2 emissions to a minimum. However, broken supply chains plus the sharp upswing in deliveries to end customers are putting pressure on even the most efficient groupage networks. This is where intelligent data management, algorithms, and AI come in: these can generate the best possible solutions with the help of mathematical models that are able to “learn” the patterns and structures present within their training data.
It all starts with logistics practices, which are built first and foremost on human expertise and the physical assets required to provide services, such as network and terminal structures. Efficiency is largely determined by what happens at the network hubs, where long-distance and short-distance transports connect. Success hinges on the logistics operatives, especially the loaders and unloaders, who have the experience required to optimize the load capacity of trailers and swap bodies, similar to playing a game of Tetris. The difference in load capacity utilization between an experienced loader versus an inexperienced loader can be as much as 15 percent. In light of demographic change, the associated lack of qualified personnel and the space shortages, it is essential that we adopt increasingly intelligent and efficient ways of dealing with the resources available to us. Together with Fraunhofer IML, DACHSER was awarded the German Logistics Award by the German Logistics Association (BVL) for @ILO at the end of 2023, a technological innovation that digitalizes groupage logistics processes to an extensive degree.
The logistics industry urgently needs digital transformation to ensure quality and to tackle challenges such as the shortage of drivers and other skilled workers.
The @ILO digital twin is nothing less than a quantum leap in groupage logistics. @ILO, which stands for Advanced Indoor Localization and Operations, can provide a comprehensive digital map of a transit terminal in real time. As identifiers, @ILO uses two-dimensional Data Matrix codes—similar to QR codes—affixed to the top of each pallet. These codes are registered by the several hundred optical scanning units on the terminal’s ceiling. In a matter of seconds and with the help of AI-based algorithms, this technology produces a digital twin—a real-time representation of all processes in the terminal, including volume measurements and item location to within one meter. Accessing this information on displays and mobile devices, forklift drivers and warehouse workers know exactly where each pallet is and where it needs to go next. This can shave anywhere from 15 to 35 percent off individual process times. The same applies for dangerous goods, which must naturally still carry regulation labeling. What’s changed here is that the new system provides this information much more clearly and efficiently than previous solutions.
@ILO is the result of more than six years of joint research carried out by DACHSER and Fraunhofer IML. DACHSER has already implemented the technology at four of its European locations and will roll it out at its larger branches in Europe over the next few years.
Transit terminals aren’t the only places AI can help provide sensible solutions. Take automation in the warehouse: automated guided vehicles (AGVs) equipped with sensor systems like cameras, lidar, and radar find their way around with the help of AI. These self-driving transporters work autonomously, performing simple repetitive tasks such as moving pallets from the warehouse to the transit terminal.
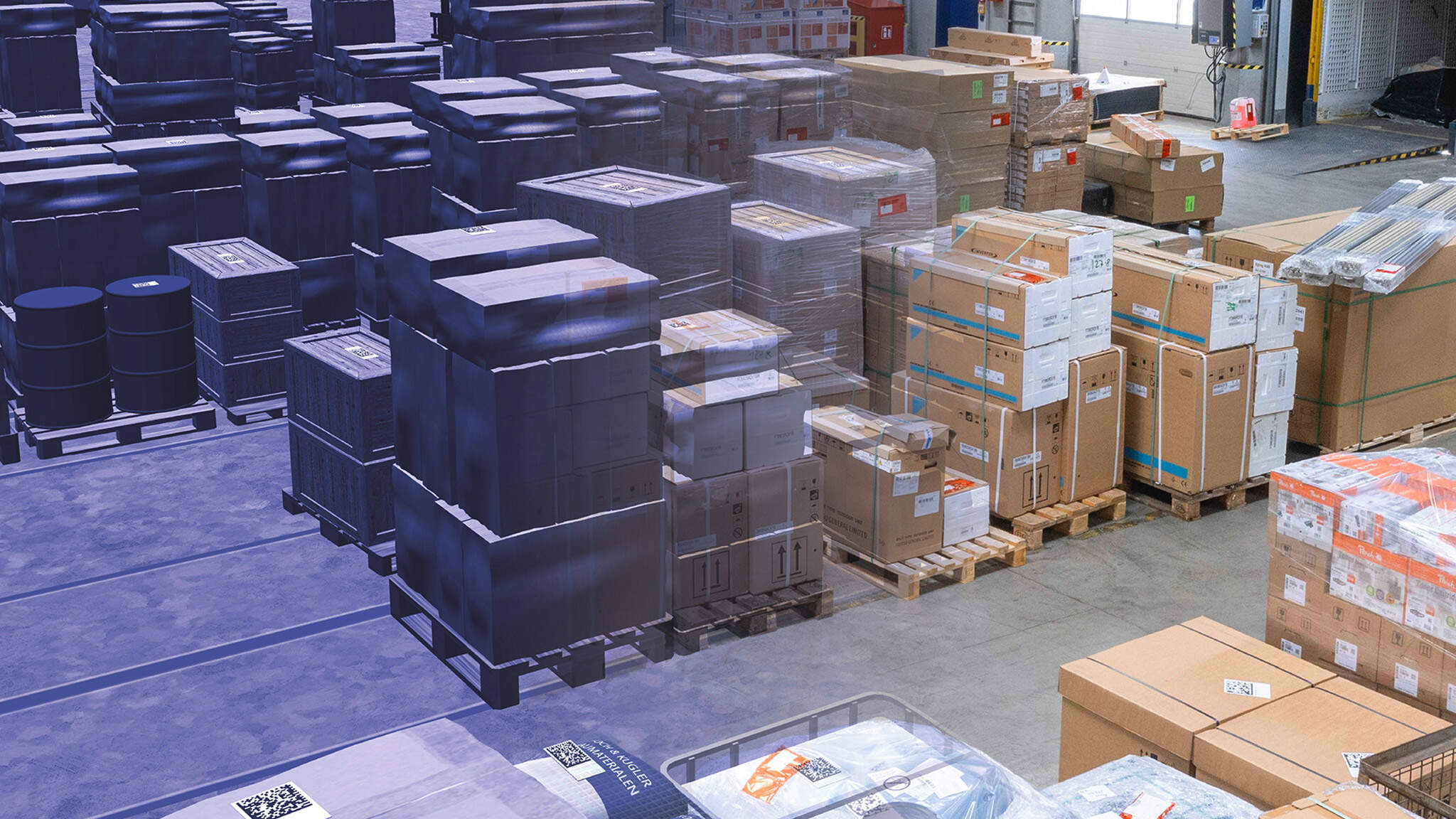
AI for intelligent planning
Another crucial factor for achieving efficiency and quality in logistics is plannability. Here, too, AI can really make a difference, as demonstrated by DACHSER’s first machine learning project: PAnDA One. This is an acronym of Predictive (P) Analytics (An) DACHSER (DA), where “One” denotes that it is the company’s first machine learning project. The PAnDA One model was specially designed to forecast inbound volumes at our European Logistics branches, providing decision-making support for capacity planning. That makes it possible to obtain suitable load capacity on the market at an early stage, or to plan resources in the transit terminal. To that end, the forecasting model provides the relevant inbound volumes up to 25 weeks in advance. PAnDA One thus gives branches another valuable tool—one that provides data to underpin the “gut feelings” of experienced operations managers and to validate the insights gleaned from discussions with customers. The technology helps people make sound decisions.
Reducing transport emissions
Sustainable practices—with their ecological, social, and economic dimensions—pave the way to a secure and economically stable future. DACHSER aims to achieve net zero CO2 emissions for its own facilities and vehicles as soon as possible. For this reason, the company established special e-mobility locations in Freiburg, Hamburg, and Malsch near Karlsruhe. These locations focus on researching and testing zero-emission battery-electric trucks and their charging infrastructure, the use and self-production of renewable electricity, and intelligent power and load management. It might not seem obvious at first, but collecting data and using it intelligently plays a key role here as well: developing reliable models and application scenarios for rolling out zero-emission short- and long-distance transports calls for data gathering on a grand scale. This is an exciting use case for DACHSER’s future application of AI.
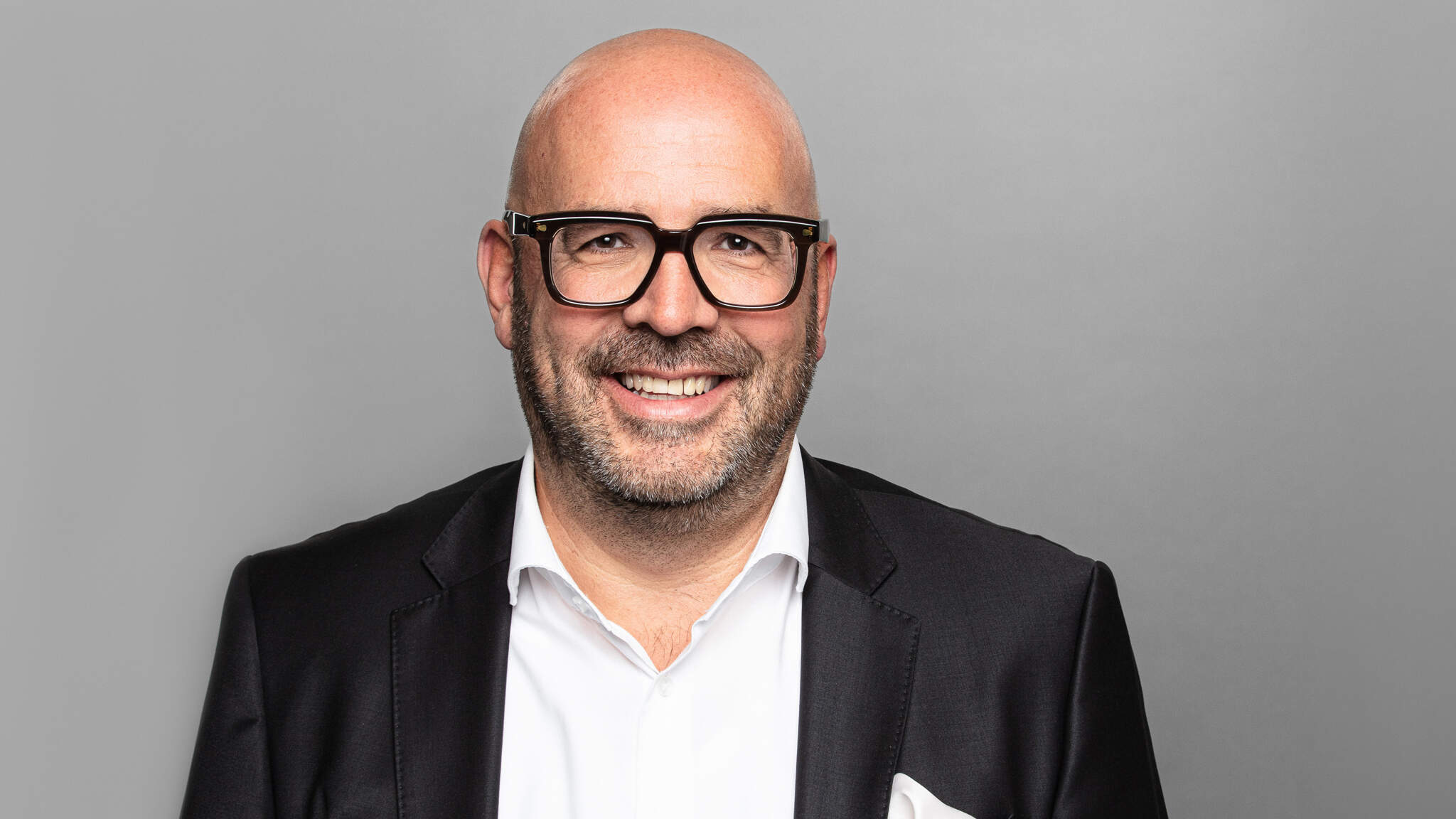
Wanted: critical thinkers
What DACHSER has learned from using AI applications is that machine learning often involves taking a trial-and-error approach. It’s about testing training data for as long as it takes to arrive at the desired degree of precision and a level of quality sufficient for the use case. In contrast to conventional coding, this calls for one thing above all else: patience. AI can also come with its share of downsides, such as loss of control, liability risks, and other challenges. That’s why it’s important to scrutinize each process critically and using human common sense. But on the whole, digital transformation offers outstanding opportunities for sustainable, future-proof development. Rather than replacing people, a sensible dose of AI and machine learning will help them make more informed and thus better decisions. Logistics is made by people, for people—and that’s not going to change. In other words, each company has what it takes to shape its own digital future.
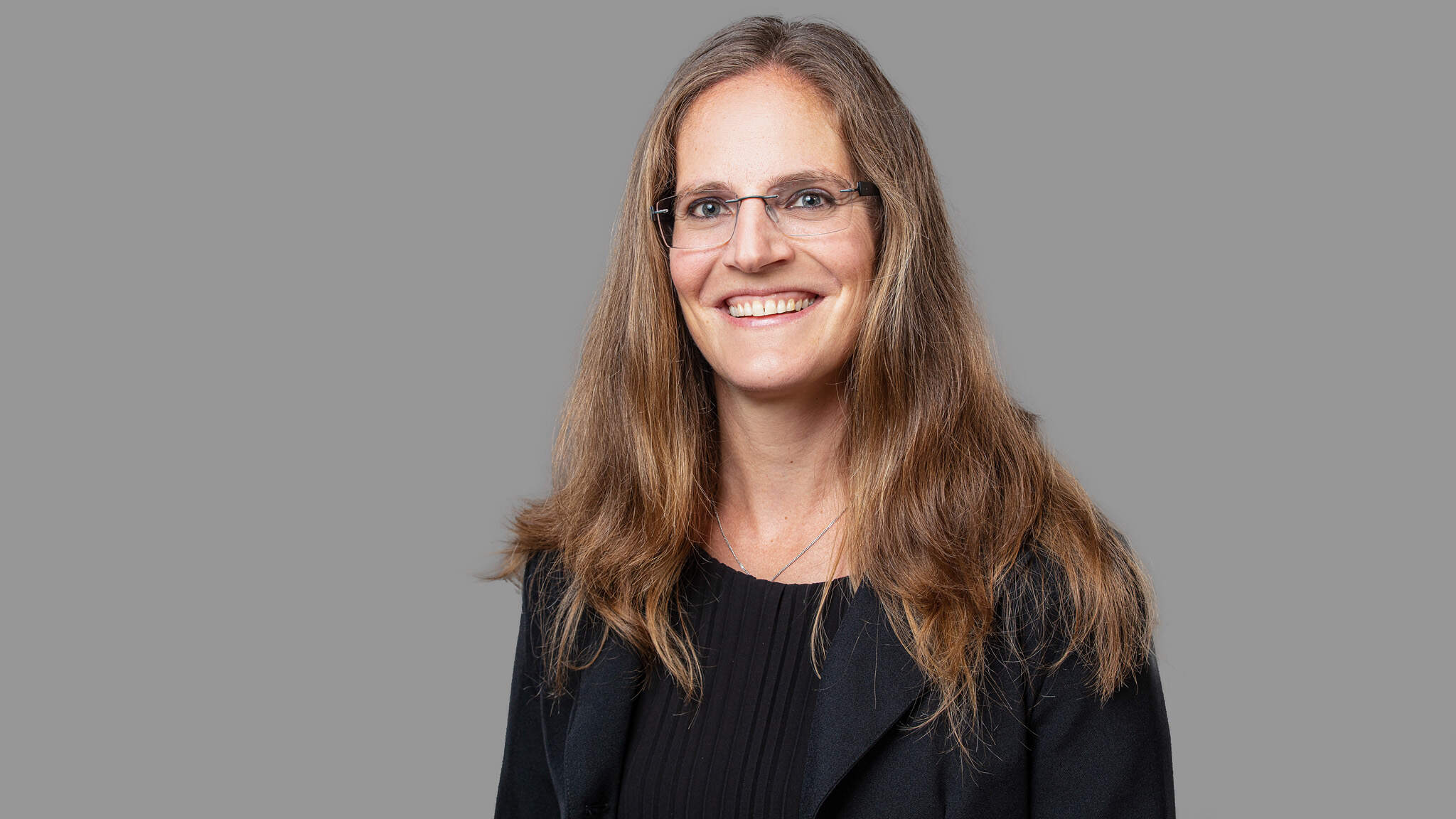