Suitable adjusting screws for successful logistics
Screws, tools, and assembly and installation material should always be delivered on time. A comprehensive direct delivery concept at Adolf Würth GmbH & Co. KG ensures that everything arrives on time across Europe. DACHSER is in charge of forwarding deliveries.
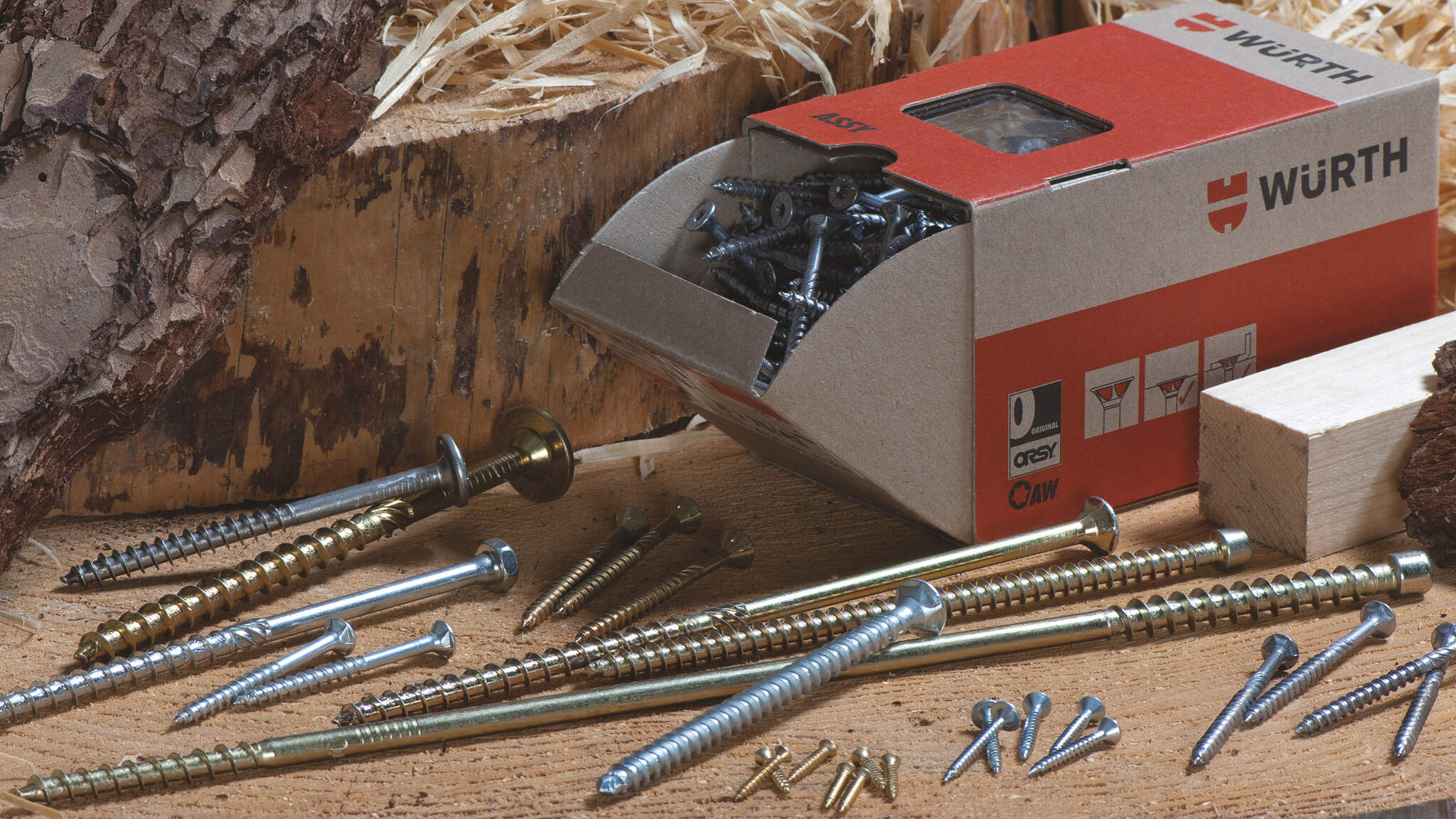
Less talk, more action - the only way to find out what the customer really needs is by “doing.” Professor Reinhold Würth believes proximity to the customer is the be-all and end-all of successful management. The figures at the wholesale company for nuts and bolts, founded in 1945 in Künzelsau, Germany, show that this philosophy pays off. What was once a two-man business has turned into the Würth Group, a global market leader that sells assembly and installation material to 3.6 million customers worldwide.
For a company with a range of over 125,000 products, a customer promise of this nature always presents a particular challenge for logistics, especially when it involves combining deliveries from different distribution points. This approach tries to ensure as far as possible that the customer does not have to wait for individual shipments coming from different directions, with different transport service providers, and on different dates. But there is a solution: direct delivery from the central warehouse in Künzelsau to customers across Europe. Jochen Höschle, in charge of the supply chain for Adolf Würth GmbH & Co. KG, explains the concept: “From the warehouse in Künzelsau, we serve customers from 23 country organizations in the north, south, east, and west of Europe. For this demanding process to run efficiently and cost-effectively, we need a high-performance, reliable, and flexible partner. And we’ve found that in DACHSER.”
Trusting cooperation
The cooperation between Würth and DACHSER began in 2006 and both partners have been gradually expanding it since 2009. DACHSER handles the transportation of palleted shipments in certain regions of Germany and to selected European countries for Würth. Every day, some 50,000 packages leave Würth’s central warehouse - that’s 75 to 80 swap bodies per day only for direct delivery to customers across Europe, and those numbers are on the rise. Tonnage growth recently amounted to 9 percent. Würth also keeps turning to DACHSER to process shipments of dangerous goods.
Marc-Oliver Bohlender, DACHSER branch manager in Öhringen, explains that over the past ten years, Würth and DACHSER have worked together in close collaboration and have made great strides in many innovations, such as in shipment tracing or in groupage structures for direct connections to customers of the individual Würth companies.
DACHSER has also partnered with them on drop shipping for many years, which connects suppliers with Würth Logistics. Würth presents a variety of logistical challenges. Höschle elaborates: “Country A might require the full delivery service, while country B needs only products from a certain sales branch, and country C needs ‘only’ slow-moving products. Everything has to be individually tailored to the needs of each European market. The customers as well as the Würth country organizations also benefited from direct deliveries from Germany. It lets us cut costs in logistics processes and frees up storage capacity at the country organizations for their future growth by reducing the amount of stock they keep on hand.”
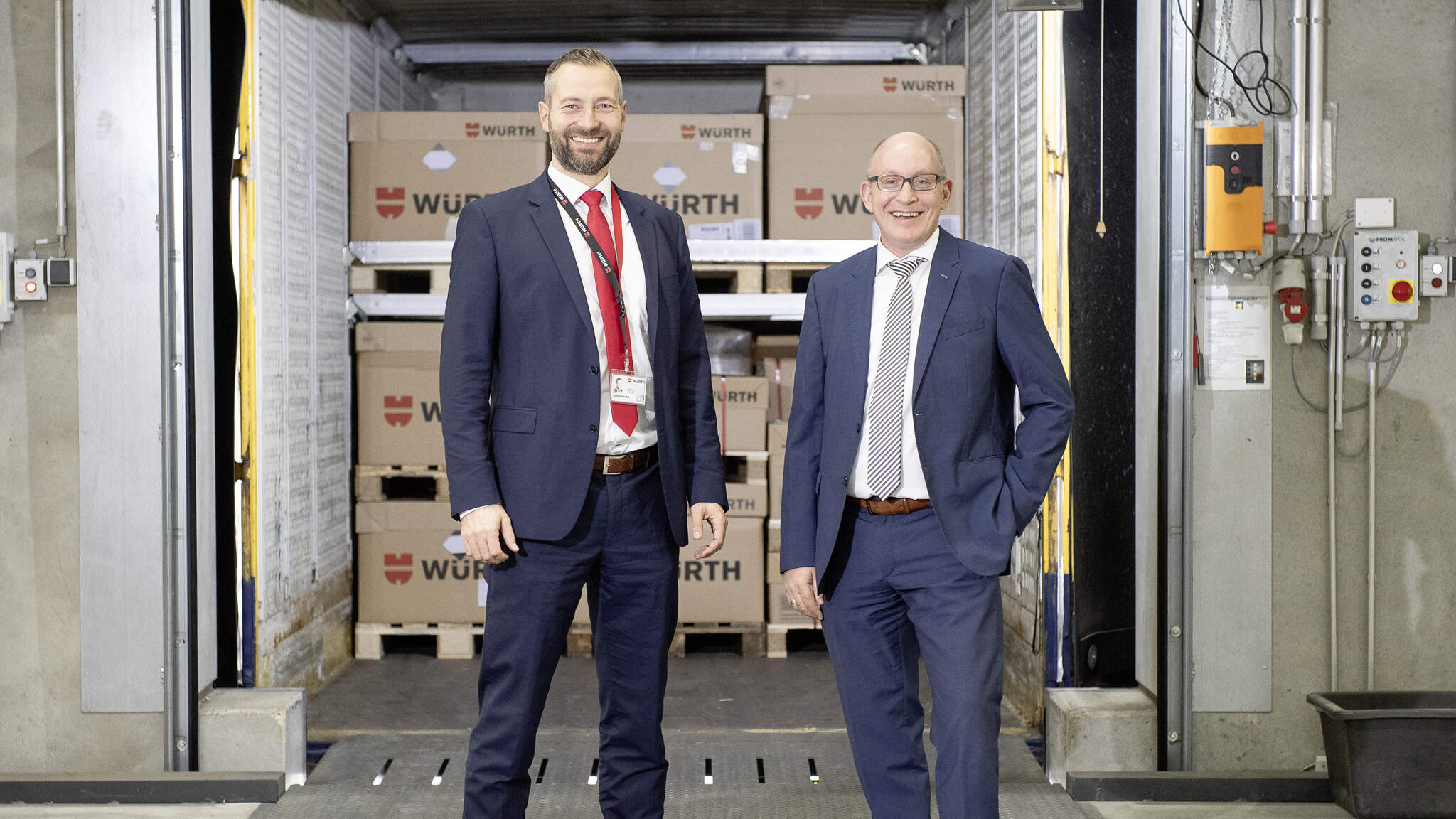
Setting up ideal processes
Würth and DACHSER are continuously improving these model processes. “Some of our numerous distribution points are still out of sync, and are located not only in Künzelsau, but in external warehouses up to 80 kilometers away,” Höschle says. The requirement of making sure everything is provided on time and on schedule is a challenge for separating or consolidating the material flow and for well-organized factory traffic. In addition, the companies always keep an eye on the roads to avoid traffic jams wherever possible or make detours. Central, automated order receipt with the highest data quality is also crucial for optimum shipment management.
A team of experts from DACHSER Öhringen and Würth are working together on topics like these. “Be it a distribution point or transport control center at Würth, scheduling or tracking & tracing at DACHSER - everything is connected to everything else,” Höschle says. Würth is currently building a new logistics center. The first shipments were sent from there at the end of November this year. This sets the course for a highly modern handling and provides the basic prerequisite for an ideal process design in the future.